Every day, founders & operators everywhere are building new technologies and companies that should us optimistic about tomorrow. My goal: champion some of these founders, companies, and industry trends. Join thousands of investors, operators, and founders on the mailing list!!
Two months ago, Solugen raised +$350M to scale their chemical production process. Such a massive Series C blew my mind, so I decided to dive in.
Solugen is truly one of the most innovative, important companies of the next decade. The content is complex, but it is a company everyone should learn about. So let’s break it down.
The Problem: Climate change is a threat to humanity…and accelerating
~15% of people surveyed globally cited climate change as a top concern. We are in a climate emergency, and ~800M people are vulnerable to the impacts of climate change.
The worst part? It is accelerating. Consider these facts:
The seven warmest years from 1880-2020 all occurred after 2014 (Source)
July 2021 was the hottest month ever (Source)
There has never been more carbon dioxide in the air than there is now (Source)

The only answer is to reduce carbon levels…but that is very complicated. People often try to change consumer habits by stressing the importance of the environment. Sadly, this just doesn’t work. Recycle bottles. Turn off lights. Ride your bike. Carpool.
People (and corporations) will not change habits at scale unless there is a legit, direct incentive to them personally (e.g., HOV lanes).
Electric vehicles are a great example. EVs only went mainstream when Elon Musk rebranded the industry. Tesla designed a car that truly beat traditional gas on performance, aesthetic, and experience. Combined with government subsidies and incentives, electric vehicles began to win over consumers AND make financial sense. Only then did EVs scale.

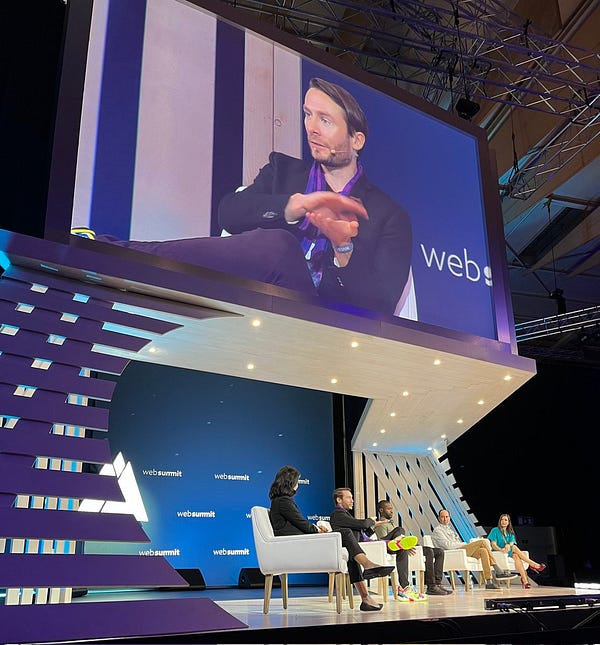
Exhibit 2: Seth Bannon on changing consumer behavior
As a result, EV growth was 40% YoY in 2019!!!! Unfortunately, it still only accounts for ~1% of global car stock. Even then, batteries are dependent on clean energy to charge, and they come with potential environment ramifications we need to solve for.
Let’s look at recycling. Sure, recycling has improved, but our process is pretty broken. ~18% of plastic is currently recycled (still too low), but only 1% of plastic (way too low) produced was made from bioplastics.
We are much more likely to succeed if we can create clean, efficient, and economically feasible ways to make plastic than if we just try to convince people to recycle. If we want to reimagine how we make plastics, we should look no further than the chemicals industry.
The chemicals industry is one of the key fundamental building blocks of the majority of products we use. Plastics. Computers. Toothpaste. They all have interdependencies.
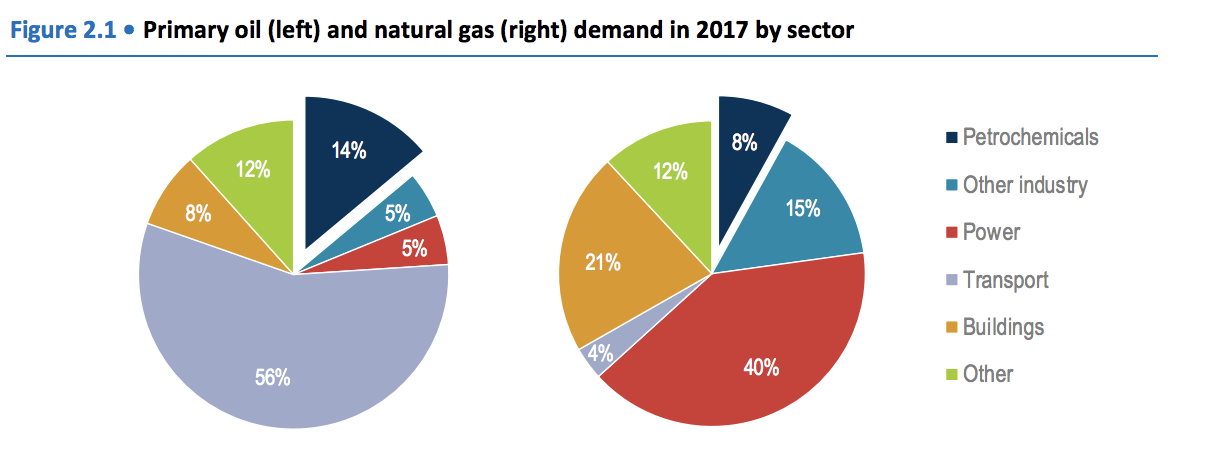
The chemical industry accounts for ~14% of global oil and 8% of global natural gas consumption. It is the third largest sector of emissions.
Let’s talk about why this industry pollutes so much.
The Context: Fermentation and Petrochemistry
There are really two main processes leveraged to produce chemicals:
Petrochemistry
Fermentation
Both processes start with what is a called a ‘feedstock.’ GreenFacts defines a feedstock as, “the raw material that is required for some industrial process.” Think of it as a low-value building block that chemistry will be performed upon.
Petrochemistry is the most common method for chemical production. By definition, it is “the branch of chemistry concerned with petroleum and natural gas, and with their refining and processing.” As a result, the feedstocks come from dirtier, non-renewable sources like coal, natural gas, and oil.
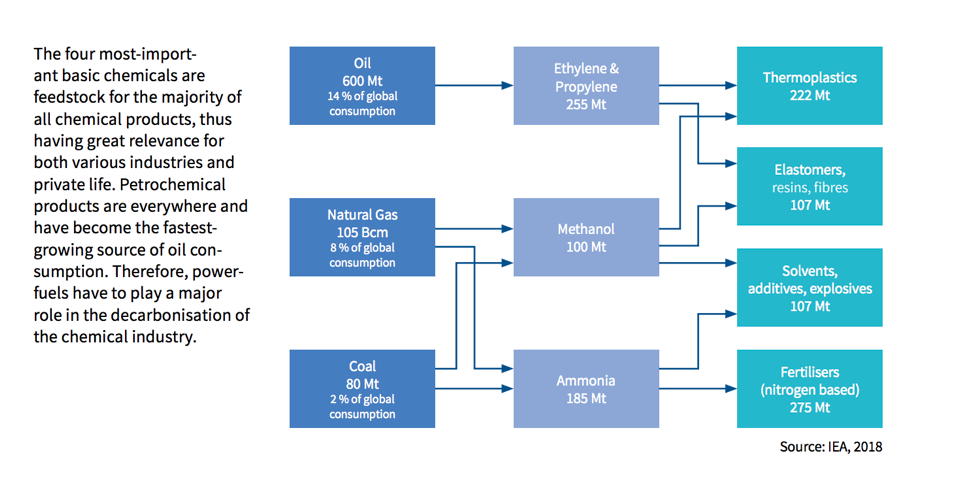
In Exhibit 4, we see a high-level view of how oil, natural gas, and coal are leveraged to produce four of the most common basic chemicals used as feedstock: ethylene, propylene, methanol, and ammonia. They create products we use daily like thermoplastics (e.g., plastic bottles), elastomers (e.g., rubber), solvents, and fertilizers.
Source of emissions #1: The entire front-end process of converting feedstock to product is fundamentally built upon a non-renewable, high-pollution foundation (feedstock).
Converting the feedstock, however, is not easy. As you can imagine, converting oil to ethylene & propylene is not a simple two-step process. It is incredibly complex, and across the entire process, chemicals are heated, separated, treated, etc.
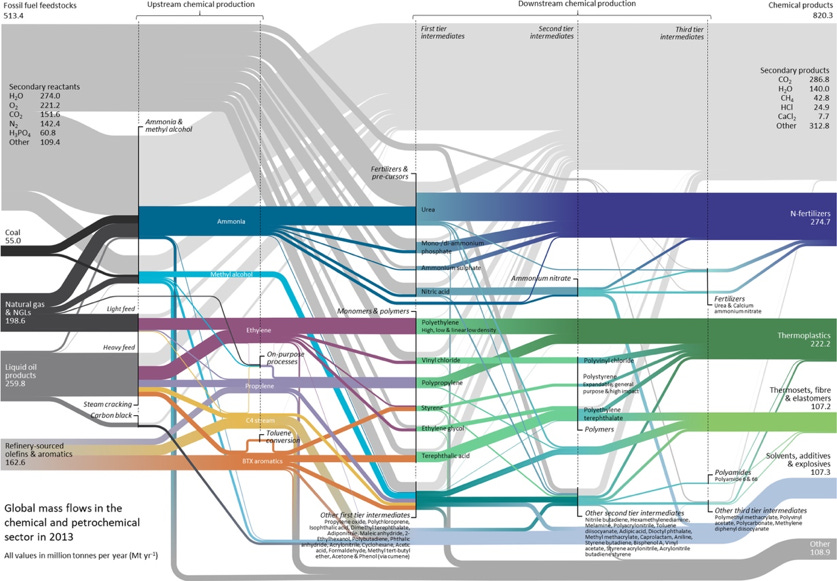
Exhibit 5 shows the path of oil, coal, natural gas, etc. across the entire chemical production process. If you think the graphic is complex, then you are not alone. That is the point of my including it.
Across the entire production process, there is an incredible amount of complexity as the original feedstock (e.g., oil) is converted, and this results in the primary output (e.g., polyethylene for thermoplastics), as well as many secondary and tertiary products that need to be handled.
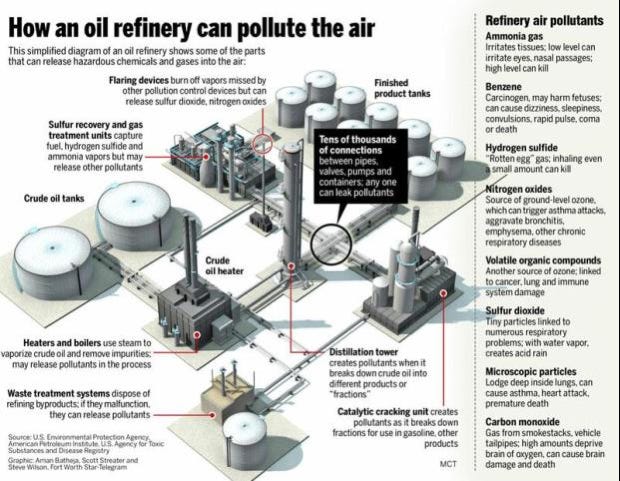
Understandably, we can see in Exhibit 6 why an oil refinery has so many parts. There are pieces fundamental to developing the product like the crude oil tanks, crude oil heater, distillation tower, and catalytic cracking units. There are also many pieces used to handle the entropy along the way like waste treatment systems, sulfur recovery and gas treatment units, and flaring devices.
Within all of these units, there are tens of thousands of connections designed to use as much of the excess products and separations as possible. Regardless of how strong we get in this process, however, there will always be a lot of pollution and waste.
Source of emissions #2: Separating secondary and tertiary products from the front-end process drives a significant amount of pollution, complexity, and waste
These separated secondary products can be sold and used for other processes. Some just need to be properly handled as waste. Most of these processes occur at highly centralized, large-scale refineries. As a result, they require a significant amount of infrastructure to simply transport and manage secondary products.
Source of emissions #3: The secondary products and waste created at highly centralized factories requires significant infrastructure and resources to transport for reuse or waste treatment
Now, up to this point, we have really only discussed the challenges with petrochemistry. We did, however, acknowledge there was another process: fermentation.
Fermentation is appealing because it solves some of the challenges of source of emissions #1: the non-renewable feedstock. Fermentation can leverage sugars as feedstock.
But fermentation has significant challenges itself, particularly in scaling. ~50% of the sugar is converted to carbon dioxide (through respiration), and the cells are living organisms. As a result, they are doing over 20,000 reactions simultaneously. The process is both inefficient and challenging to scale at the industrial levels required.
In summary, our current process of chemical development primarily leverages petrochemistry which has three main problems / sources of emissions:
The Solution: Combining the best of fermentation and petrochemistry with the Bioforge
Solugen has created a high-throughput, renewable solution to the sources of emissions above by leveraging the best attributes of fermentation and petrochemistry to create a new, chemi-enzymatic process. Let me explain.
I have broken the production process into their two main 'stages':
The Enzymatic Phase - Leveraging fermentation, cell-free manufacturing, and renewable feedstock to develop the two primary inputs for the Bioforge
The Thermo-chemical Phase - Leveraging the strengths of thermo-chemistry in the proprietary Bioforge to convert the primary inputs to the desired output, consisting of two main processes: A) the Enzyme Reactor and B) the Metal Reactor
The Enzymatic Phase
First, let's start with the Enzymatic Phase. The focus of this phase is to create the two primary inputs required for the enzyme reactor:
The Renewable Feedstock
High-density enzymes
The renewable feedstock is straightforward. Solugen can just purchase this. In their case, they use corn as the base. No physical corn, but actually, it is a corn-based liquid (think Ethanol...or even maple syrup!).
Creating the high-density enzymes, however, is much more complex. First, a few definitions:
An enzyme is “a substance that acts as a catalyst in living organisms.”
A catalyst is “a substance that increases the rate of a chemical reaction without itself undergoing any permanent chemical change.”
Basically, the enzyme is a substance that increases the rate of a chemical reaction within a living organism. By controlling the enzymes, Solugen can control the output of the reaction and produce chemicals.
The traditional approach would be synthetic biology. In synthetic biology, engineers redesign “organisms for useful purposes by engineering them to have new abilities.” Synthetic biology redesigns the entire cell. Within the cell, however, there are thousands of enzymes, but there are really only a handful of enzymes really needed.
An analogy: Imagine you have a huge bag of M&Ms. You ONLY like red M&Ms. To make a big batch of M&M cookies for a holiday party, you would need to buy 10 huge bags of M&Ms. You would then toss the yellow, blue, etc. M&Ms. It is inefficient. It is wasteful. But what if you could buy just one huge bag of red M&Ms? Way more efficient, right?
This is the magic of cell-free manufacturing. In that analogy, the bag of M&Ms is the cell. The M&Ms represent enzymes. The bag (cell) holds many different M&Ms (enzymes), but only a the red M&Ms (certain enzymes) are really important to baking the cookies (the chemical reaction).
So this is what Solugen does:
They take an input (in this case Biomass / sugar)
Leverage proprietary software (similar to CRISPR) to engineer the cells to create very specific enzymes
Leverage large fermentation tanks to produce the enzymes
The result: Extremely affordable, high-density enzymes specifically design for the chemical being created.
Here are two quick examples of the magnitude of impact (Note: CTO Sean Hunt breaks down this entire process in the Built with Biology podcast):
Merck produces enzymes at $100,000 per kilogram vs. Solugen $10 per kilogram (10,000x improvement)
10,000 gallon bubble column has the same throughput of a 500,000 fermenter (50x improvement)
And get this. The isolated enzymes are not living cells. So they are less complex and not producing carbon dioxide.
The Thermo-Chemical Phase
As a result of the enzymatic phase, there are two primary outputs to be fed into the Thermo-chemical stage (as inputs): i) the high-density enzymes and ii) the renewable feedstock.
At this stage, the two outputs enter the Bioforge. If it sounds intense, it is.

Exhibit 11: Overview of the Bioforge
Exhibit 11 shows how large the Bioforge really is. This is where the true magic happens.
Admittedly, we know a little less about the details within the Bioforge (for obvious reasons), but there are a two main points to understand:
The Bioforge Contains two main processes:
a. Enzyme Reactor
b. Metal Reactor
The importance of software throughout
First, the high-density enzymes and renewable feedstock enter the Enzyme Reactor. The process here is straightforward from a logic perspective. If you recall, the enzyme is the catalyst. Once exposed to the feedstock, the reaction will begin taking place.
The logic is straightforward, but it is important to note, the execution is not, particularly at scale. Solugen has spent years fine tuning both the reactor design, as well as software to help manage the flow of the inputs (renewable feedstock & enzymes) and air.
The second process is the metal reactor. Here the outputs from the enzyme reactor are fed into what is known as a 'trickle-bed reactor'

Exhibit 12 shows an example (not Solugen's) of a trickle reactor. Fundamentally, the outputs of the enzyme reactor are fed into the metal reactor and 'showered' over the 'packing'. In this case, the 'packing' is metal (e.g., Gold). By showering the outputs over the metal, they begin to react, and new substances are formed.
These are the fundamental concepts behind the two processes within the Bioforge, but it should be no surprise there are insane amounts of complexity within both, especially as they scale.

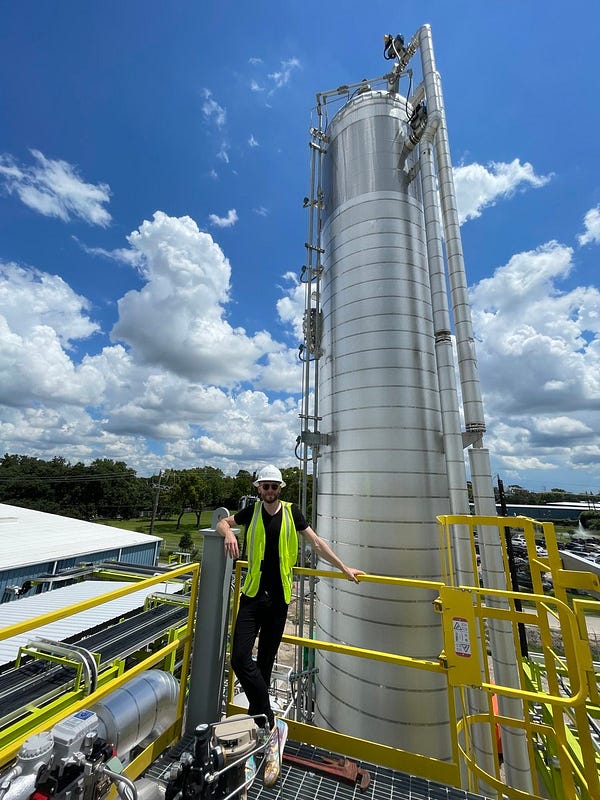
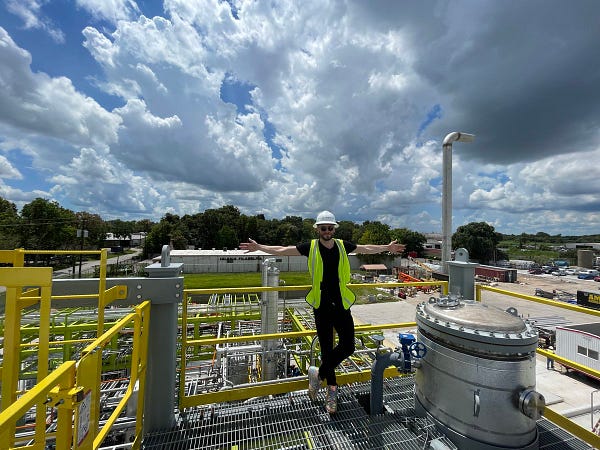
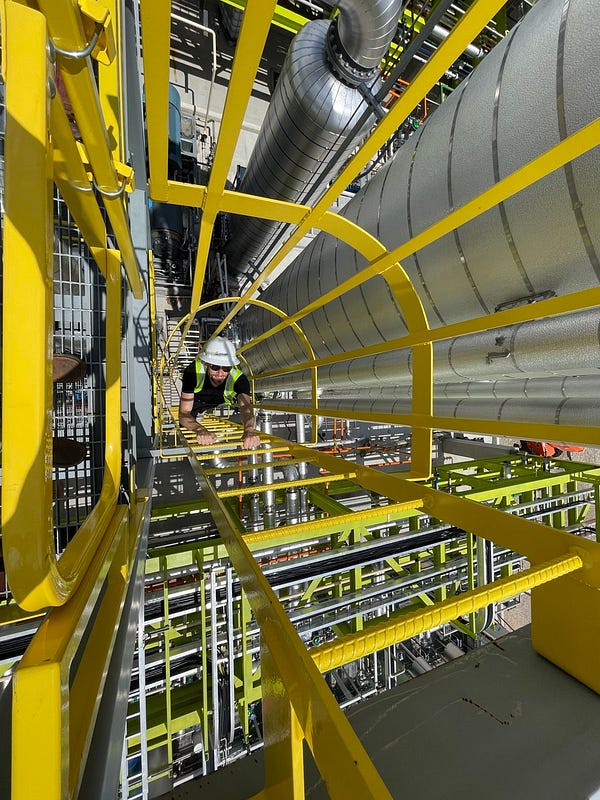
Exhibit 13: Scaling the Bioforge
Exhibit 13 shows how quickly Solugen has scaled over the years. That's a 30x increase in pure height, and between other optimizations (e.g., higher density enzymes, fermentation tanks), it is likely the scale is a few factors higher than that.
The true 'secret sauce' underpinning all of this is Solugen's software. Solugen is taking on traditional chemical companies, but it is doing it with biology and software engineering.
Software is a critical cost advantage for Solugen in many places, but here are three main areas:
Engineering Biomass to produce specific enzymes (Enzymatic phase)
Managing the inputs of the enzyme reactor with high precision at scale (Thermo-chemical phase)
Predicting and managing the 'showering' and exposure of chemicals to the metal packing in the metal reactor (Thermo-chemical phase)
While these may seem simple, they are truly cost advantages for Solugen. Not only did they reinvent the entire production process (e.g., Chemi-Enzymatic), but their excellence in software is allow them to scale, ultimately improving the unit economics.
The Results: Building Carbon-Negative Chemical Production
If you recall, I outlined three main sources of emissions in the beginning:
Source of emissions #1: The entire front-end process of converting feedstock to product is fundamentally built a non-renewable, high-pollution foundation (feedstock)
Source of emissions #2: Separating secondary and tertiary products from the front-end process drives a significant amount of pollution, complexity, and waste
Source of emissions #3: The secondary products and waste created at highly centralized factories requires significant infrastructure and resources to transport for reuse or waste treatment
Each one of these sources are a problem, and Solugen's new approach has solved all three of these problems.
The renewable feedstock and high-density enzymes solves for source of emissions #1. In addition, the process does not kick off toxic secondary and tertiary chemicals, so the new approach solves all emissions related to source of emissions #2. Finally, if there are no secondary and tertiary chemicals to transport, then Solugen indirectly solves source of emissions #3.
In summary, Solugen solves all three buckets of emissions, and as a result, Solugen is both the world's first carbon negative chemical plant, as well as Houston's first permitted facility with no wastewater discharge or air emissions. This is monumental.
But the results do not just stop there. The products work well. Solugen already sold a brand of clean wipes to Diamond Wipes. Now, they are growing swiftly in other areas like water treatment. The immediate success led to a $357M Series C, designed to quickly accelerate growth.
Not only is the strong product accelerating this growth, but Solugen actually has a cost structure advantage. We have highlighted the significant inefficiencies in separating chemicals (e.g., secondary and tertiary chemicals). This is expensive, and for each step a chemical takes throughout that complex process, there is a margin hit. It makes sense. Each step in the value chain will demand some margin to separate, transport, or treat these chemicals. Solugen removes that, giving them a significant margin advantage.
In summary, Solugen is already proving out 1) the strong product, 2) the superior unit economics, and 3) the environmental impact. This is the perfect recipe for wide scale impact and change.
Conclusion: The Future Vision of Solugen
There are four major implications of Solugen:
Emissions
Safety
Agility
Localized production
First, the carbon impacts of Solugen are something we have covered in great length. Solugen estimates it could apply their process to ~90% of chemicals produced today. Replacing current emissions with a carbon neutral (potentially carbon negative) approach that offers superior unit economics could be one of the largest Climate Change solves to date.
Second, chemical plant explosions and incidences are actually quite frequent. By leveraging enzymes instead of highly flammable chemicals, the Bioforge is noticeably safer than the typical petrochemical plant.
Third, the Bioforge increases supply chain agility. This is a little less obvious. What do I mean by this? The Bioforge can be adjusted to create a variety of chemicals. Typically, it may take weeks, months, or longer to repurpose a chemical plant. With the Bioforge, they can adjust the enzymes and software within days. This allows for Solugen to quickly pivot & adjust systems to increase chemical production to meet market needs.
Finally, Solugen's solution could lead to localize production. Rather than massive, centralized refineries in Texas, each region (e.g., city, state, factory) could have a localized Bioforge producing chemicals. The Bioforge is much smaller, and it can be repurposed. All it requires is shipments of 1) renewable feedstock and 2) high-density enzymes.
With a quick software update and a truckload of both inputs, a Bioforge can be setup directly next to a customer, water treatment plant, etc. and create localized jobs, decreased transportation costs (and emissions), and mitigate supply chain risks.
The final vision: Dramatically reduce emissions from chemical production by building a localized, carbon negative Bioforge in each region.
It is impossible to overstate how huge of a breakthrough Solugen could be.
Appendix
One pager
Market factors
Growth
Corporate responsibility - There is an increasing pressure on corporations to act on climate change. Over 200 companies have committed to net zero emissions by 2040, and the list is growing. These early pledges may seem hollow, but they are creating a market for climate tech. By creating the market, suppliers have a financial incentive to invest in cleaner tech. For example, Maersk announced their first zero emissions cargo ships. This trend will continue, and it will be a strong tailwind for Solugen
Regulation - Corporate responsibility is the private sector trending to cleaner solutions, but in parallel, the public sector will be as well. The US government helped Tesla significantly early on with subsidies. It is reasonable that they will do the same for clean technologies across the board, especially Solugen, which can improve safety, reduce oil dependency, and increase supply chain strength (w/ localization)
Uncertain
Carbon capture - Climate tech is not just focused on reducing carbon emissions. A second common theme is actually capturing existing carbon. Recently, a popular study on carbon capture was shared by David Friedberg and Elad Gil. Carbon capture still seems to be nascent and have scalability issues. If these are solved and applied to the chemicals industry, it is reasonable that it will provide a significant lift to the market
Challenges
International feedstock supply - One challenge in scaling alternative chemical production will be global supply chain of feedstock. In international markets like China & India, it is proving to be more challenging than the US to acquire renewable feedstock (e.g., corn-based ethanol). This will not be a dealbreaker by any means, but until solutions are created, there could be some headwinds
Market sizing
Source #1 (Statista): ~$4T in 2019; ~40% of market dominated by China; declining slightly
Source #2 (Research and Markets): ~$3.8T in 2021 growing to ~$4.3T in 2025 at a ~4% CAGR
Source #3 (American Chemistry): Global chemical output increasing
By combining the sources, it is reasonable to assume that the market is in the ~$4T range with moderate growth of ~3-5%.
Competition
Solugen competes against a variety of players. Incumbent chemical companies. Emerging climate tech companies. Etc.
On the climate tech side, Solugen has the largest scope and the technological lead.
On the incumbent side, Solugen almost exclusively competes against Chinese manufacturers of molecules like HEDP, PBTC, BHMT, DETA, EDTA, THPS, AEEA, etc.